Preparation Process of Nanoscale Ammonium Metatungstate
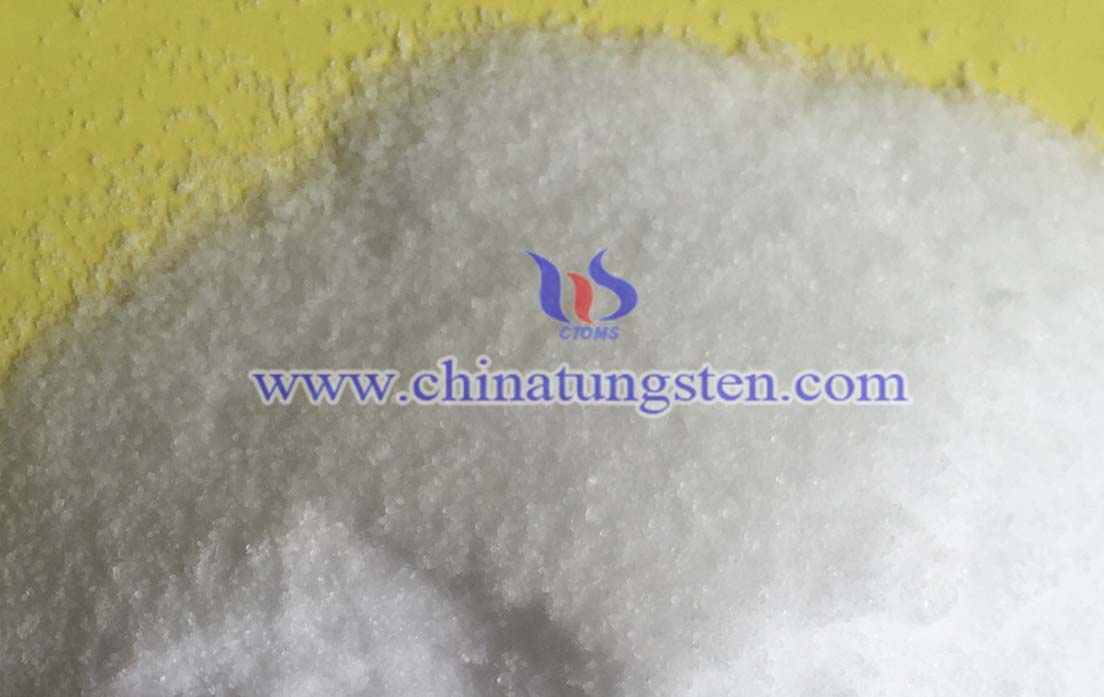
Nanoscale ammonium metatungstate (AMT, particle size < 100nm) exhibits exceptional performance in catalysts, battery materials, and photocatalysts due to its high specific surface area, excellent chemical activity, and unique physicochemical properties. Compared to traditional micron-scale AMT, nanoscale AMT significantly enhances material functionality and application efficiency due to its small size effect, quantum effect, and high surface energy.
The preparation processes for nanoscale AMT are as follows:
1. Sol-Gel Method
Working Principle: The sol-gel method involves adding surfactants (e.g., polyethylene glycol or sodium dodecyl sulfate) to an AMT solution to regulate the colloidization process, forming uniform nanoscale gel particles, followed by drying and heat treatment to obtain nanoscale AMT particles.
Technical Features:
• Process Flow:
1. React sodium tungstate (Na₂WO₄) with acid to form an AMT precursor solution.
2. Add surfactants to control the viscosity and surface tension of the solution, forming a sol.
3. Adjust pH, temperature, and stirring speed to promote gelation, forming nanoscale particle precursors.
4. Perform low-temperature drying and heat treatment (typically < 200°C) to obtain high-purity nanoscale AMT powder.
• Advantages:
o Controllable Particle Size: By adjusting the type and concentration of surfactants, AMT particle sizes can be precisely controlled (typically 10-50 nm).
o High Uniformity: The sol-gel method produces nanoparticles with uniform morphology and excellent dispersibility.
o Versatility: Different crystal forms and structures of AMT can be prepared by modifying reaction conditions.
• Challenges:
o Process Complexity: Precise control of multiple reaction conditions (e.g., pH, temperature, and surfactant concentration) increases process complexity.
o High Cost: The use of surfactants and subsequent heat treatment equipment increases production costs.
o Limited Yield: The sol-gel method is typically suited for small-scale preparation, requiring optimization for large-scale production.
2. Spray Pyrolysis Method
Working Principle: The spray pyrolysis method involves atomizing an AMT precursor solution into fine droplets using a high-pressure nozzle, followed by rapid decomposition in a low-temperature pyrolysis furnace (300-400°C) to directly produce nanoscale AMT powder.
Technical Features:
• Process Flow:
1. Prepare an AMT precursor solution (typically using sodium tungstate as the raw material, acidified to form the precursor).
2. Atomize the solution into micron-sized droplets using a spray device.
3. The droplets rapidly evaporate and decompose in the pyrolysis furnace, forming nanoscale AMT particles.
4. Collect the nanoscale powder using a cyclone separator or filter.
• Advantages:
o High Efficiency and Speed: The spray pyrolysis method enables continuous production, suitable for large-scale preparation.
o Uniform Particle Size: By controlling the spray droplet size and pyrolysis temperature, nanoscale AMT with a narrow particle size distribution (20-80 nm) can be obtained.
o Low Energy Consumption: The pyrolysis temperature (300-400°C) is lower than traditional high-temperature roasting processes, resulting in significant energy savings.
• Challenges:
o High Equipment Requirements: The spray device and pyrolysis furnace require precise control to ensure droplet uniformity and pyrolysis efficiency.
o Byproduct Handling: The pyrolysis process may generate small amounts of volatile gases, necessitating a supporting exhaust gas treatment system.
o Cost Issues: High initial equipment investment and maintenance costs require process optimization to reduce overall expenses.