Moisture Content of Ammonium Metatungstate
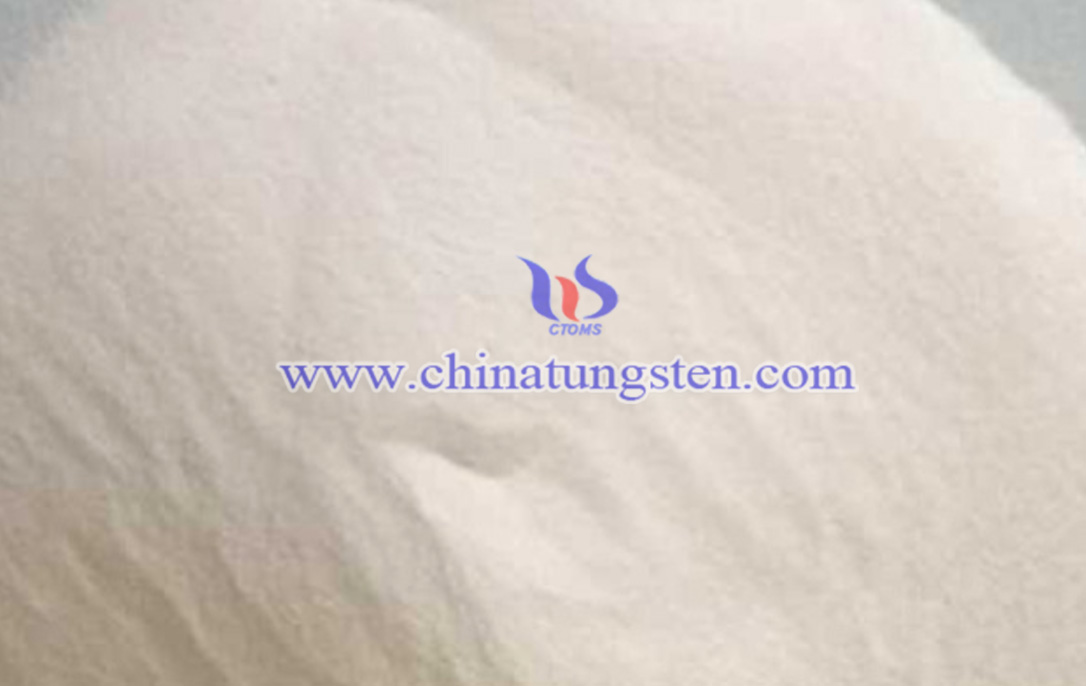
Significance of Moisture Content in Ammonium Metatungstate
Since AMT molecules contain crystalline water, the moisture content directly affects its chemical stability and storage conditions. Additionally, it plays a crucial role in determining its solubility, thermal decomposition behavior, and processing characteristics in subsequent applications. Therefore, accurate measurement and control of moisture content are essential for ensuring the quality and performance of AMT. One of the most common methods for moisture content analysis is thermogravimetric analysis (TGA), which measures the weight loss of a sample as a function of temperature under controlled heating conditions.
Thermal Behavior of AMT and Moisture Loss
During TGA analysis, AMT exhibits distinct thermal decomposition stages:
• 50-150°C: AMT gradually loses its crystalline water, resulting in the first weight loss phase. This step corresponds to the release of physically bound water within the hydrate.
• Above 300°C: AMT undergoes chemical decomposition, progressively transforming into tungsten trioxide (WO₃). This stage involves structural breakdown and the volatilization of certain components, leading to further mass reduction.
By analyzing the percentage of weight loss at each stage on the TGA curve, the moisture content of AMT can be accurately determined. Typically, industrial-grade AMT has a moisture content controlled within the 5%-10% range, which ensures a balance between performance, processing efficiency, and cost-effectiveness.
Effects of Moisture Content on AMT Stability and Processing
• Excessive moisture (>10%):
o Can negatively affect storage stability, causing hygroscopic clumping and potential localized chemical reactions, which reduce purity and usability.
o During thermal processing, higher moisture content leads to increased volatilization, potentially affecting process consistency and final product uniformity.
• Insufficient moisture ( < 5% ):
o May indicate over-dehydration during production, potentially disrupting the crystal structure integrity of AMT.
To maintain optimal moisture content, drying conditions (temperature, duration, and humidity control) are carefully adjusted in production. TGA results are used to verify compliance with specifications. Additionally, TGA data can be complemented with other analytical techniques (e.g., infrared spectroscopy) to further confirm the presence of moisture and assess its impact on AMT’s properties. This comprehensive approach helps improve product quality and enhances its performance in industrial applications.