나노스케일 메타텅스텐산암모늄 제조 공정
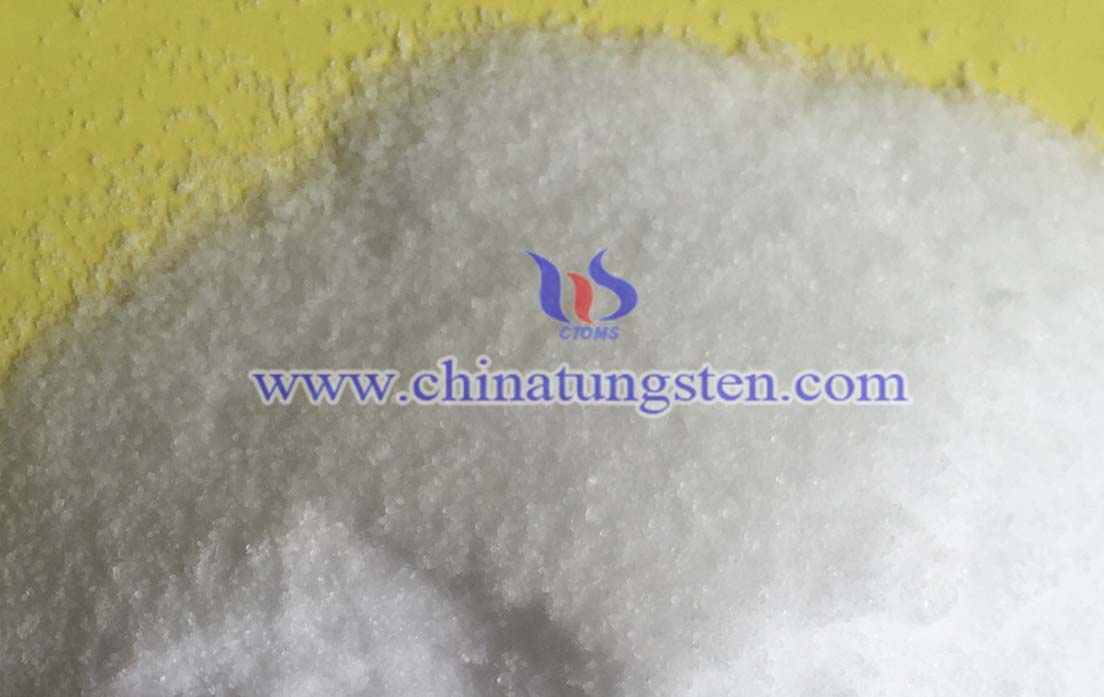
나노스케일 메타텅스텐산암모늄(AMT, 입자 크기 <100 nm)은 높은 비표면적, 우수한 화학적 활성, 독특한 물리화학적 특성으로 인해 촉매, 배터리 재료, 광촉매 등의 분야에서 탁월한 성능을 발휘합니다. 전통적인 마이크론 스케일 AMT와 비교하여, 나노스케일 AMT는 작은 크기 효과, 양자 효과, 높은 표면 에너지로 인해 재료의 기능성과 응용 효율을 크게 향상시킵니다.
나노스케일 AMT의 제조 공정은 다음과 같습니다:
1. 졸-겔법
작동 원리: 졸-겔법은 AMT 용액에 계면활성제(예: 폴리에틸렌글리콜 또는 도데실황산나트륨)를 첨가하여 콜로이드화 과정을 조절하여 균일한 나노스케일 겔 입자를 형성한 후, 건조 및 열처리를 통해 나노 AMT 입자를 얻습니다.
• 공정 흐름:
1. 텅스텐산나트륨(Na₂WO₄)을 산과 반응시켜 AMT 전구체 용액을 생성합니다.
2. 계면활성제를 첨가하여 용액의 점도와 표면 장력을 조절하여 졸을 형성합니다.
3. pH 값, 온도, 교반 속도를 조정하여 겔화를 촉진하고 나노스케일 입자 전구체를 형성합니다.
4. 저온 건조 및 열처리(보통 <200℃)를 통해 고순도 나노 AMT 분말을 얻습니다.
• 장점:
o 입자 크기 제어 가능: 계면활성제의 종류와 농도를 조정하여 AMT 입자 크기(보통 10-50 nm)를 정밀하게 제어할 수 있습니다.
o 높은 균일성: 졸-겔법은 형태가 균일하고 분산성이 우수한 나노입자를 생성합니다.
o 다양성: 반응 조건을 변경하여 다양한 결정 형태와 구조의 AMT를 제조할 수 있습니다.
• 도전 과제:
o 공정 복잡성: pH, 온도, 계면활성제 농도 등 다단계 반응 조건을 정밀하게 제어해야 하므로 공정 복잡성이 증가합니다.
o 높은 비용: 계면활성제와 후속 열처리 장비의 사용으로 생산 비용이 증가합니다.
o 제한된 생산량: 졸-겔법은 일반적으로 소규모 제조에 적합하며, 대규모 생산에는 최적화가 필요합니다.
2. 스프레이 열분해법
작동 원리: 스프레이 열분해법은 AMT 전구체 용액을 고압 노즐로 미세한 액적에 분무한 후, 저온 열분해로(300-400℃)에서 빠르게 분해하여 나노스케일 AMT 분말을 직접 생성합니다.
• 공정 흐름:
1. AMT 전구체 용액을 준비합니다(보통 텅스텐산나트륨을 원료로 하여 산성화하여 생성).
2. 스프레이 장치를 사용하여 용액을 마이크론 크기의 액적으로 분무합니다.
3. 액적은 열분해로에서 빠르게 증발하고 분해되어 나노 AMT 입자를 형성합니다.
4. 사이클론 분리기 또는 필터를 사용하여 나노 분말을 수집합니다.
• 장점:
o 고효율 및 신속성: 스프레이 열분해법은 연속 생산이 가능하여 대규모 제조에 적합합니다.
o 균일한 입자 크기: 스프레이 액적 크기와 열분해 온도를 조절하여 입자 크기 분포가 좁은 나노 AMT(20-80 nm)를 얻을 수 있습니다.
o 낮은 에너지 소비: 열분해 온도(300-400℃)는 전통적인 고온 소성 공정보다 낮아 에너지 절감 효과가 뚜렷합니다.
• 도전 과제:
o 높은 장비 요구 사항: 스프레이 장치와 열분해로는 액적 균일성과 열분해 효율을 보장하기 위해 정밀한 제어가 필요합니다.
o 부산물 처리: 열분해 과정에서 소량의 휘발성 가스가 발생할 수 있으며, 배기 가스 처리 시스템이 필요합니다.
o 비용 문제: 초기 장비 투자와 유지보수 비용이 높아 공정 최적화를 통해 전체 비용을 줄여야 합니다.